
Incense Holder
Functional Sculpture
Client
mahota.design
Timeline
Ongoing
Background
This project is an ongoing effort to explore how digital design and manufacturing techniques can be combined with hand craftsmanship to create ceramic products that are formally congruent and repeatable while being aesthetically unique and handmade.
These incense holders are designed to be engaged with as functional sculpture. The ceramic material and process have been unapologetically presented in the final form with the hope that the user is able to experience a more considered and meaningful connection to the material and maker.

Inspiration
I’ve always been fascinated by the seemingly endless possibilities for surface finishes in ceramics and had been searching for the perfect project to explore exceptionally contrasting textures. Coincidentally, a friend recently asked if I’d ever thought about making incense holders. The idea immediately clicked, and I knew it was the perfect vessel to dive into this exploration with.

Via Fire and Earth Pottery

Via Old Forge Creations
I started by ideating concepts that I felt could elevate the experience of burning incense and would encourage the user to take notice of the material characteristics.
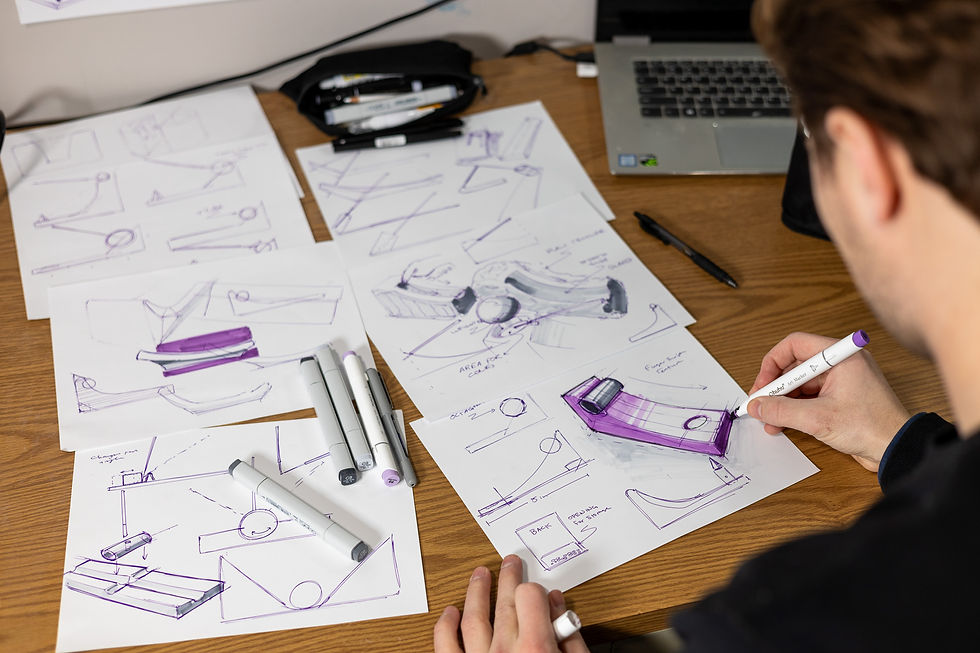
Prototyping
I used 3d printing and hand-building to evaluate some early form concepts in person.
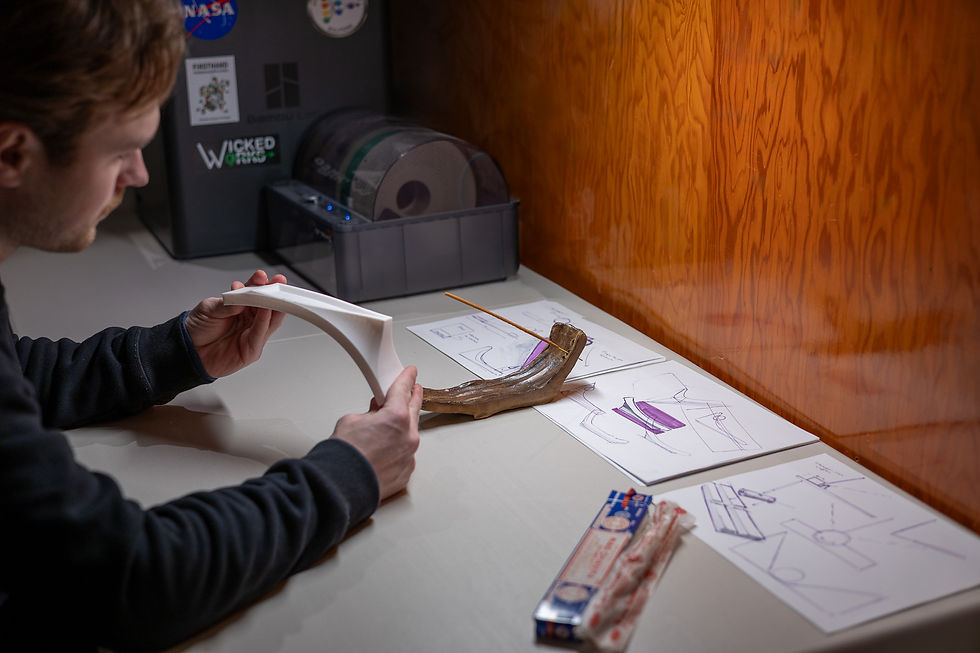
Manufacturing
After reviewing the 3d prints, I tweaked the proportions and changed the base to transition more smoothly out of the foot ring. I then created a press-mold system in Fusion360 and poured the first plaster mold.


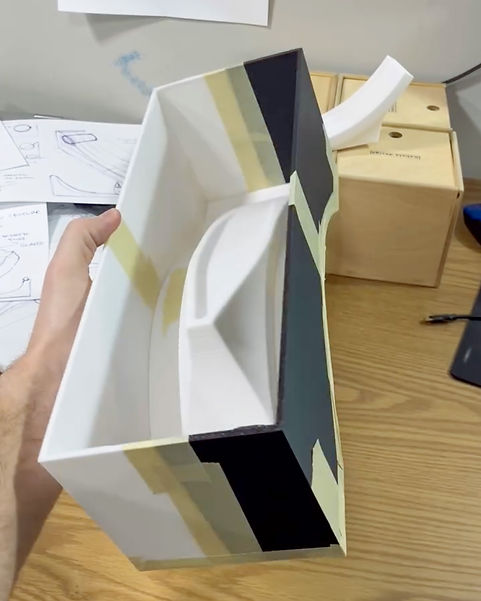

I press-molded the first few test pieces and adding a unique hand texture to each one.


Resolving Issues
The industry standard for maximum recommended wall thickness in ceramic goods is ~1/2in, with thicker pieces risking cracking in the kiln due to excessive moisture retention. At ~2in in the thickest dimension, the incense holders were far beyond that and as a result, all of the early test split apart in the kiln.


I was aware this could happen, but I was against changing the holder design because the uniquely weighty form was important to the final user experience and aesthetic I was looking for. So I tried fixing the issue with a couple other tricks. First, I experimented with changing of make-up of the clay mix I was using and added different amounts of grog (a ceramic additive used to minimize shrinkage). Second, I built a "dehydration chamber" using a small dehumidifier to store the holders in for a few days after being de-molded.


The combination of these two things worked like a charm and I was able to move forward with the chunky design! I glazed a few final prototypes in a variety of different glazes, oxide washes, and engobes to explore different CMF options.


Current State
Here are some images of the existing prototypes. I sent them each out to be user tested and am currently in the process of a slight re-design based on feedback and to improve manufacturability. The final product will include custom luxury packaging and a sample pack of local incense sticks.